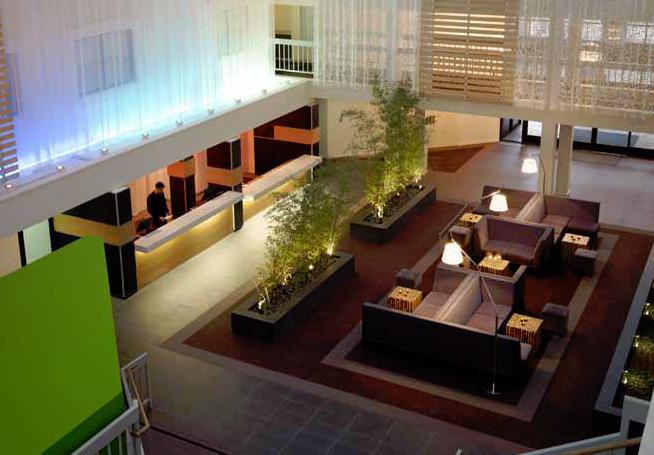
San Francisco is the home of construction makeovers, and one contractor in particular, GCI General Contractors, has taken it to a fine art, as Alan Swaby learns.
Anyone familiar with the geography of San Francisco will know that with water on three sides, there is precious little opportunity for new buildings to be erected. As such, the construction industry in the city itself is focused on renovation and refurbishment.
In good times the process can be savage, with buildings being stripped to the bone and new exteriors and interiors built onto the core. But these are not good times, and building owners and tenants are keen to spend as little as possible while still giving their surroundings a face-lift.
In a sense, this suits the local firm of GCI General Contractors down to the ground. Almost by accident, it has carved a niche and a name for itself through the extent of its recycling and its ability to maximize the re-use of existing building elements and materials.
“As long ago as 1999,” says company president James Jenkins, “GCI was recycling much of the material that was being taken out of redevelopment projects—long before the industry took notice of it in the quest to get LEED certification. These days we’re often hitting the 85-90 percent mark in recycling ceilings, doors, carpet, misc. metals and even sheetrock.”
Back then, this emphasis on reusing material could have been influenced by the economics of the work the business was doing. Set up by Pete Goldsmith in 1992 with the support of his wife, the couple worked for the first few years out of their home after Goldsmith left Dinwiddie Construction to go it alone. On one level, GCI was doing well with just a handful of staff overseeing $15-20 million of business. But Goldsmith knew that he needed help to move to the next stage just about the time that Jenkins was looking for a new opportunity. Jenkins had 15 years of experience working in commercial construction in San Francisco after returning to the US following a short career overseas with the oil company Schlumberger, and he was ready for a change.
“We were introduced by a mutual associate,” says Jenkins, “and initially I thought that GCI was just too small to give me what I was looking for. But Pete is a very likeable and persuasive guy.”
The persuasion was well justified. Since joining in 2001, the business was doubling in size every four years until the recession hit in 2008. Not surprisingly, the numbers have slipped back, but GCI is now an established force in San Francisco and the Bay Area.
“It’s interesting how unexpected factors play into your hands,” says Jenkins. “First it was recycling and then the 2001 anthrax attacks occurred and caused panic when any white powder or residue was discovered. As you can imagine, there is plenty of white powder associated with construction work, but in that climate, project sites were being shut down regularly.”
As it happens, GCI was using a HEPA filter-based air cleaning system to give workers a dust-free environment in which to work and to eliminate paint and glue smells for their clients prior to move-in. Not only did this keep its projects going, but when LEED brought the need for indoor air quality to the fore, once again GCI was already ahead of the pack. In fact, it’s now something of the go-to contractor for LEED certification projects—particularly when Gold or Platinum levels are being sought. When clients such as the Natural Resources Defense Council, the Environmental Defense Fund, The Wilderness Society and ClimateWorks Foundation are coming to you to manage their building construction, others take notice. Jenkins estimates that GCI is responsible for one-fifth of all LEED-CI interior projects in San Francisco.
“LEED has become very trendy,” says Jenkins, “and there’s a lot of green-wash spoken by firms wanting to jump on the bandwagon. But knowledgeable clients are aware of this and hire GCI to help them reach their sustainability goals.”
These days, Jenkins reckons that there is no price penalty to be paid for building to the basic LEED standards. “We do this automatically,” he says. “It’s only for the higher levels where there is a premium, but even then the premium will eventually be paid for in improved building efficiency, lower operating costs, and improved employee productivity.” GCI recently renovated its own offices at a cost less than a standard tenant improvement budget and its offices were certified LEED-CI Gold in early 2010.
In fact, GCI is often called in to act as consultants, helping architects and clients to achieve extra points toward certification without major cost impacts. GCI recently completed the local law offices of O’Melveny & Myers which is currently the largest law office in the country to achieve LEED-CI Gold certification. The ClimateWorks Foundation project was certified LEED-CI Platinum and received the highest LEED point total ever in California and the third highest in the world. Other pre-construction services include pre-lease feasibility studies, building surveys, and finding suitable premises based on criteria that potential tenants have set.
With precious little hands-on work—and definitely no self-performance—GCI remains lean, with just project managers and field superintendents on the payroll. Even at its height, the company never had more than 55 staff members.
Instead, it employs working principals who still roll their sleeves up and manage projects, project managers and assistants at the top of their game, and site superintendents who know what they want from subcontractors and how best to get it. By insisting on their own personal levels of satisfaction during construction, they can be pretty sure that during the handover walkthrough the possibility of defects that need attention is zero or mighty close to it. With this attention to detail, GCI has recently delivered over 250,000 SF of office space with zero defects.
GCI is currently investing heavily in new building information modeling (BIM) technology but Jenkins thinks it will be money well spent. “BIM has proved itself in designing and constructing new buildings, but there is nobody we know using this technology in the tenant improvement and interiors market. We see this as a way to continue to give us the edge we seek over the competition. The technology could lead us to find new ways to use materials more efficiently and to further minimize waste. In today’s climate, that could make all the difference.”
GCI’s reputation is ensuring it gets opportunities to pitch for new work, but it’s still sometimes a battle getting clients to think beyond commodity to value added. “We try to convince them to go back to basics and put money into durable and reusable items and features rather than frivolities. It’s not always the message they want to hear, but we think it’s still the right one.” www.gci-sf.com